TSMaster is a domestic automotive bus tool chain software platform developed by TOSUN, which is a professional tool for all-round automotive bus design, simulation, analysis, diagnosis and calibration, and supports the whole system development process from demand analysis to system realization. TSMaster software can connect, configure and control all TOSUN hardware interface card, realize the automotive bus monitoring, simulation, diagnosis, calibration, BootLoader, I/O control, measurement and testing, EOL and other occasions of functional requirements. And support Vector, Kvaser, PCAN, Intepace, Zhou Ligong bus series hardware and mainstream instruments on the market, can realize multi-hardware, multi-channel joint simulation, test. TSMaster software users are more and more, for the user in the process of using the problems raised, we will be regularly sorted out for everyone to refer to and learn. Follow the editor to see what Q&A answers this issue.
01, TSMaster CAN FD related
1. Q: Is there a function in TSMaster to enable configuration of TDC (Time Delay Compensation for Data Field Transmission) for CAN FD? Or is it enabled by default?
A:TDC(Transmission Delay Compensation) under CAN FD of TSMaster is enabled by default, if not enabled, it can't send/receive normally under FD mode.
2、Q:What is the default value of TDC's offect?
A: This offect setting value in TSMaster is calculated dynamically according to the baud rate, it is a ratio, not a fixed value.
What is Loop delay loop delay?
In the "mining" process, the CAN transceiver undergoes two conversions: the Transmitter converts a sequence of 0 and 1 digital levels to differential levels; the Receiver converts the differential levels to a sequence of 0 and 1 digital levels. Because the conversion takes time, there is bound to be a physical delay. See Figure 1, where the ECU sends a frame. level changes on the TX and Rx pins: the digital level change on the Rx is delayed by a small amount of time.
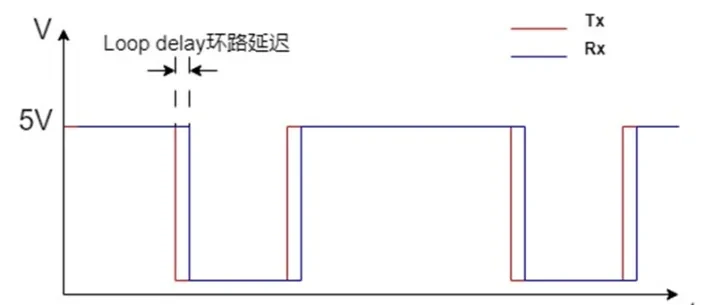
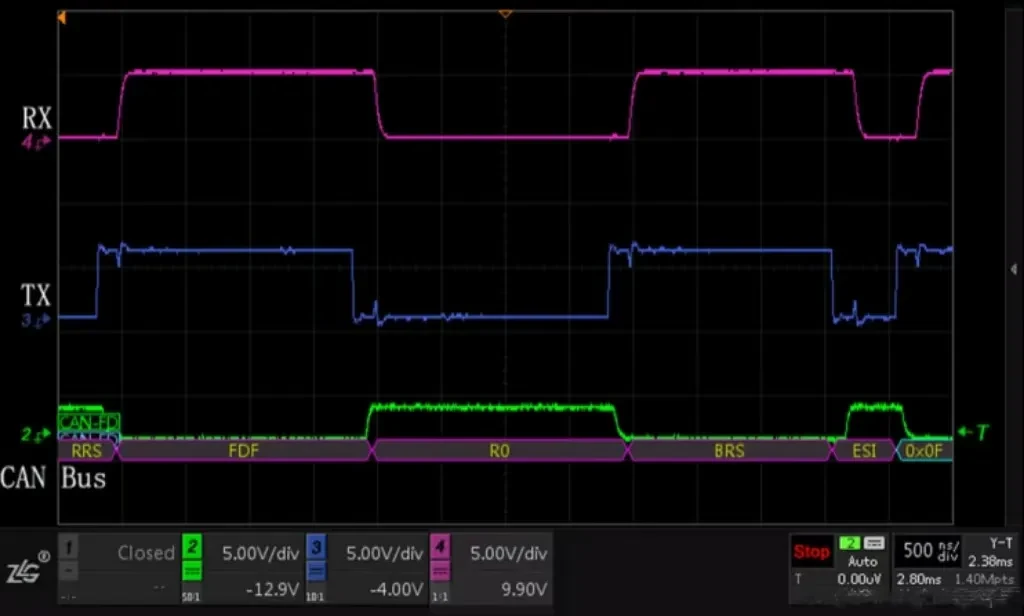
What is TDC?
TDC is: Transceiver Delay Compensation Transceiver Delay Compensation.
In the CAN FD data segment, if a faster Bit Rate is used (BRS bits enabled), resulting in a shorter bit time, the delay caused by the LOCAL CAN transceiver loop delay will be greater than Phase_Seg1 (see Figure 3, time segment time period before the sampling point): assuming that the Loop delay loop delay is 255 nanoseconds, if the CAN FD frame data segment Bit Rate is greater than or equal to 4Mhz, i.e., a Bit Time is less than or equal to 250 nanoseconds, which results in the detection of a bit error bit error. transceiver loop delay The transceiver loop delay limits the Bit Rate bit rate of the CAN FD frame data segment.
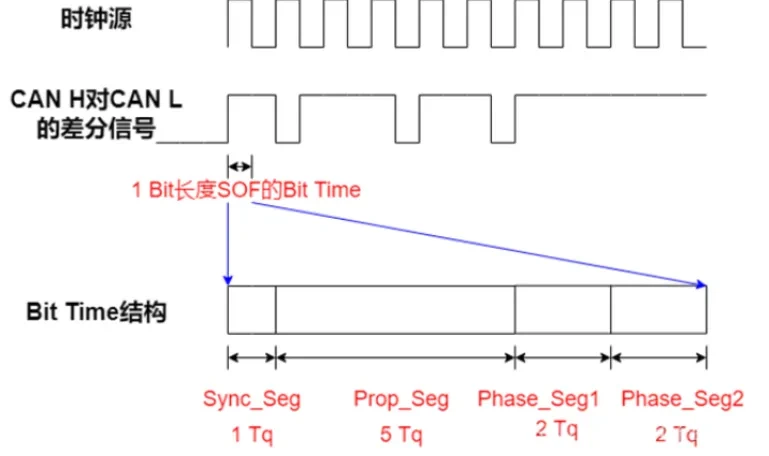
Therefore, to overcome this limitation, the TDC (Transceiver Delay Compensation) function has been introduced, i.e., in the data segment of the CAN FD frame, the transmitter shall use a new sample point, SSP (Secondary Sample Point), while ignoring the SP (sample point) of the transceiver loop delay. SSP (Secondary Sample Point) of the transceiver loop delay transceiver loop delay is ignored.
Secondary Sample Point The second sample point consists of a transceiver loop delay transceiver loop delay and a configurable transceiver delay compensation offset transceiver delay compensation offset.
Transceiver loop delay The transceiver loop delay is measured between the edge from the EDL bit (same as the FDF bit) to the next bit r0, corresponding to the transmit bit edge and the receive bit edge, in each transmit frame (see Figure 4, Figure 5). The measured loop delay is not sufficient for defining the secondary sample point as it is related to the bit edges.
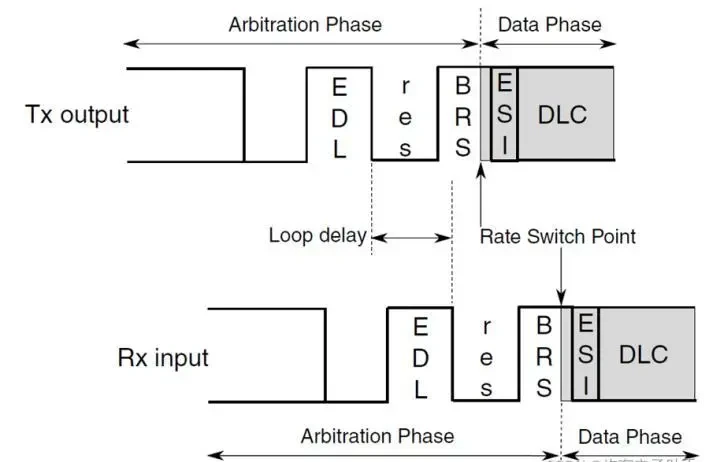
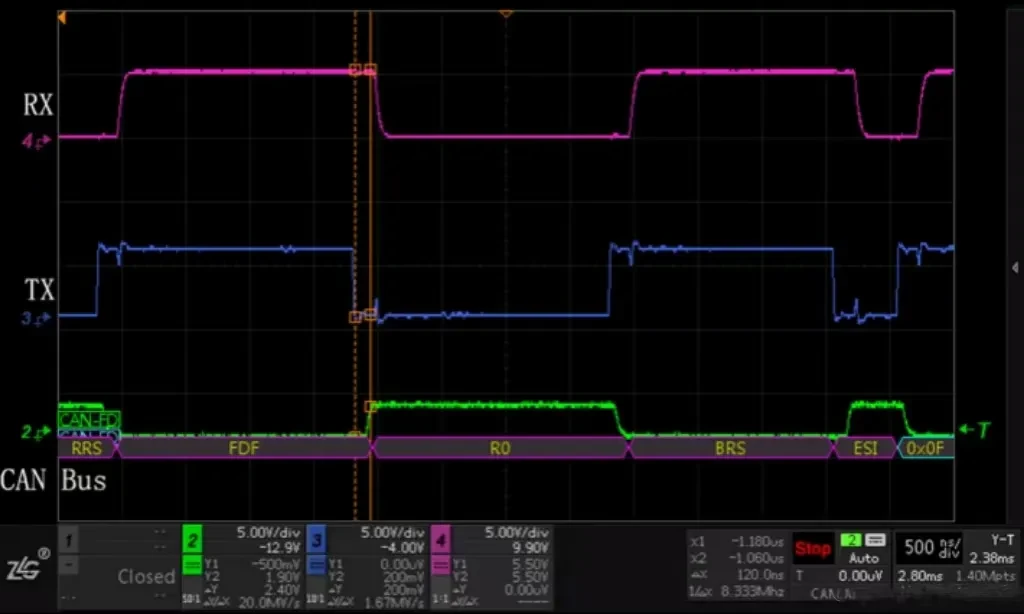
Transceiver delay compensation offset The transceiver delay compensation offset is used to shift the secondary sample point from an edge to a midpoint within bit time, away from its edge. Therefore, the offset value cannot be greater than the bit time of the data phase.
If the secondary sample point is set very close to the CAN bit edge (see Figure 3, Sync_Seg field), problems may occur during bit sampling in the data phase. For the TDC to work reliably, the offset must use the optimal setting. To ensure that bit sampling is performed in the optimal area, TDC offset is recommended to refer to the following equation, refer to Figure 3.
Offset = Phase_Seg1 + Prop_Seg + 2
Figure 6 below shows the SSP position when these settings are used.
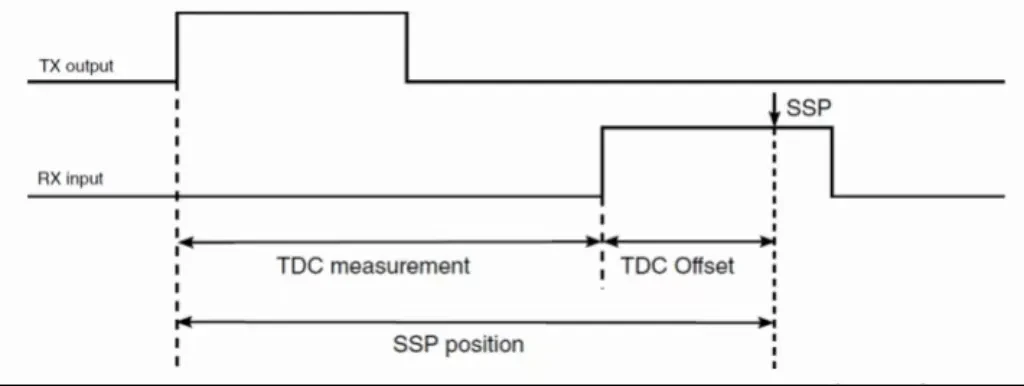
Transceiver Delay Compensation Enable Condition
The above description is summarized as follows:
Condition 1: The frame must be a CAN FD frame (not applicable to classic CAN frames because the bit time is much larger than the Loop Delay) with the BRS bit enabled (higher bit rate in the data segment than in the arbitration segment), and the SSP acts on the data segment of the CAN FD frame;
Condition 2: TDC applies only to CAN FD frames sent by the ECU, not to CAN FD frames received by the ECU.
* The content of the above dry trivia sharing is derived from the Internet.
02. TSMaster LIN message related
1. Q: What is the maximum delay time supported for LIN message sending?
A: The maximum support of 255ms is a hardware level limitation. This is how it is currently designed.

2、Q:Please tell me why deploying with scheduling table will report a checksum error, but using separate sending is not reporting an error?
A: It has been verified that there is an error in the checking algorithm from the node ECU, so it is a normal report message to have a checksum error in the scheduling table run.
And when a single frame is sent, it is true that no checksum is performed so no error is triggered.
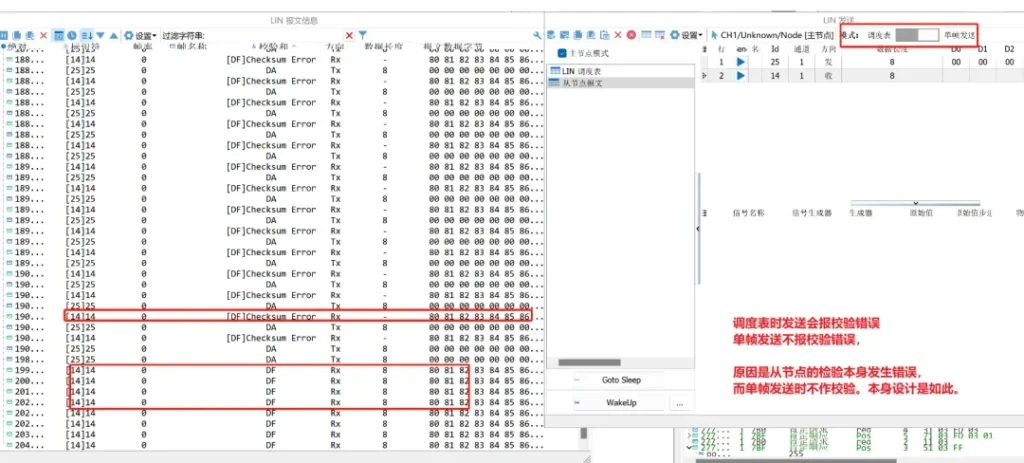
3、Q:What is the situation that after sending a message with TSMaster as the master node, the received message shows receive data timeout, but occasionally it can receive a few frames of data again?
A: First of all, from the TSMaster can only see the phenomenon of occasionally receiving a few frames of data, the specific cause of the analysis need to use an oscilloscope to analyze the waveform of the LIN message, the following two waveforms were measured by the customer anomalous message, as well as our simulation of a normal message sent to the waveform, through the comparison of the customer can be seen in the data section of the stop bit pull a very long time, from which you can judge the customer's ecu response to the data is likely to be a problem. The probability is that the customer's ecu response is problematic.

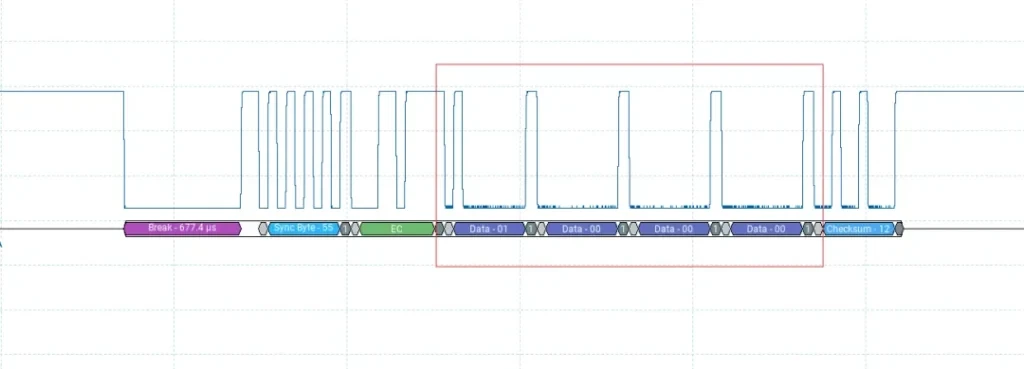
4. Q: What is indicated in square brackets [ ] of LIN message identifier? For example, [50]10

A:This is lin's PID, Protect ID, and ID unique correspondence, you can check the table correspondence.
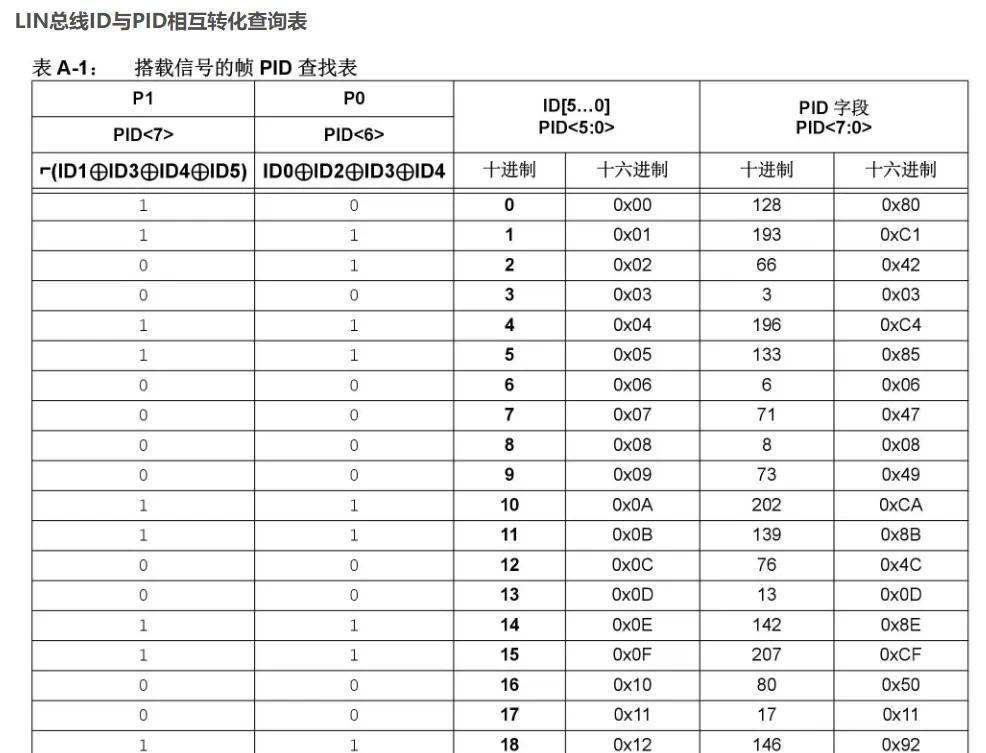
The above are a few common questions about the two major blocks of TSMaster CAN FD related and LIN message related, which have been answered and organized in detail. If you have any doubts in using TSMaster software, you can pay attention to TOSUN public number and leave a message or private message at the end of the article, we will be happy to help you solve the problem.
Note: TOSUN Technical Support Email:support@tosunai.cnWe welcome inquiries! (Company and contact information must be indicated)